ریخته گری سرامیک شل:
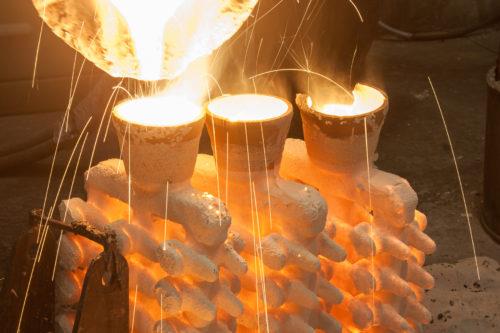
ریخته گری سرامیک شل (Ceramic Shell Casting) ریخته گری سرامیک شل یک فرآیند پیشرفته در ریخته گری دقیق (Investment Casting) است که برای تولید قطعات فلزی با ابعاد دقیق و سطحی صاف استفاده میشود. این روش به ویژه برای قطعات پیچیده و کاربردهای صنعتی با دمای بالا (مانند توربینهای گازی، قطعات هوافضا و پزشکی) مناسب است.
مراحل فرآیند ریخته گری سرامیک شل 1. ساخت مدل مومی: – ابتدا یک الگوی مومی دقیق از قطعه مورد نظر ساخته میشود. – این مدل ممکن است به صورت دستی یا با استفاده از چاپ سه بعدی تولید شود.
2. ساخت پوسته سرامیکی: – مدل مومی در یک سوسپانسیون سرامیکی (معمولاً حاوی سیلیکا یا آلومینا) غوطه ور میشود. – پس از هر بار غوطه وری، مدل با دانه های سرامیکی (مثل ذرات زیرکونیا یا ماسه سیلیس) پوشش داده میشود. – این فرآیند ۵ تا ۱۰ بار تکرار میشود تا پوسته سرامیکی ضخیم و مستحکم ایجاد شود.
3. خروج موم (ذوب موم): – پوسته سرامیکی در کوره قرار میگیرد تا موم ذوب و خارج شود. – این مرحله به پوسته اجازه میدهد تا مقاومت حرارتی بالایی پیدا کند.
4. ریخته گری فلز: – فلز مذاب (مانند فولاد، سوپرآلیاژها یا آلومینیوم) درون پوسته سرامیکی خالی ریخته میشود. – پس از سرد شدن فلز، پوسته سرامیکی با ضربه یا شستشو شکسته و جدا میشود.
5. پرداخت نهایی: – قطعه فلزی به دست آمده ممکن است نیاز به عملیات حرارتی، ماشینکاری یا پولیش داشته باشد.
مزایای روش سرامیک شل – دقت ابعادی بالا: امکان تولید قطعات با تلرانسهای بسیار کم (تا ±۰.۰۵ میلیمتر). – سطح صاف: کاهش نیاز به پرداخت نهایی. – انعطاف پذیری در طراحی: ساخت قطعات با هندسه های پیچیده و دیواره های نازک. – مقاومت حرارتی: مناسب برای فلزات با نقطه ذوب بالا (مانند تیتانیوم و نیکل). – کاهش ضایعات: بازیافت موم و سرامیک امکانپذیر است.
کاربردها – صنعت هوافضا: پرههای توربین، قطعات موتور. – پزشکی: ایمپلنتها و ابزارهای جراحی. – خودروسازی: قطعات موتور و سیستمهای اگزوز. – جواهرسازی: ساخت قطعات تزئینی با جزئیات بالا.
مواد مورد استفاده در پوسته سرامیکی – لایه های اولیه: سوسپانسیونهای ریزدانه (مثل سیلیکا کلوئیدی). – لایه های بیرونی: ماسه های درشت تر (زیرکونیا یا ماسه سیلیس) برای استحکام بیشتر. – چسبهای شیمیایی: برای اتصال بهتر لایه ها (مانند سیلیکات سدیم).
معایب احتمالی – زمانبر بودن: فرآیند ساخت پوسته و خشک کردن آن ممکن است چند روز طول بکشد.
– هزینه بالا: برای تولید انبوه، نیاز به تجهیزات و مواد ویژه است.
– حساسیت به ترکخوردگی: پوسته ممکن است در اثر تنشهای حرارتی ترک بخورد.
-این روش به دلیل دقت و کیفیت بالا، جایگزین مناسبی برای روشهای سنتی ریخته گری در صنایع پیشرفته محسوب میشود.
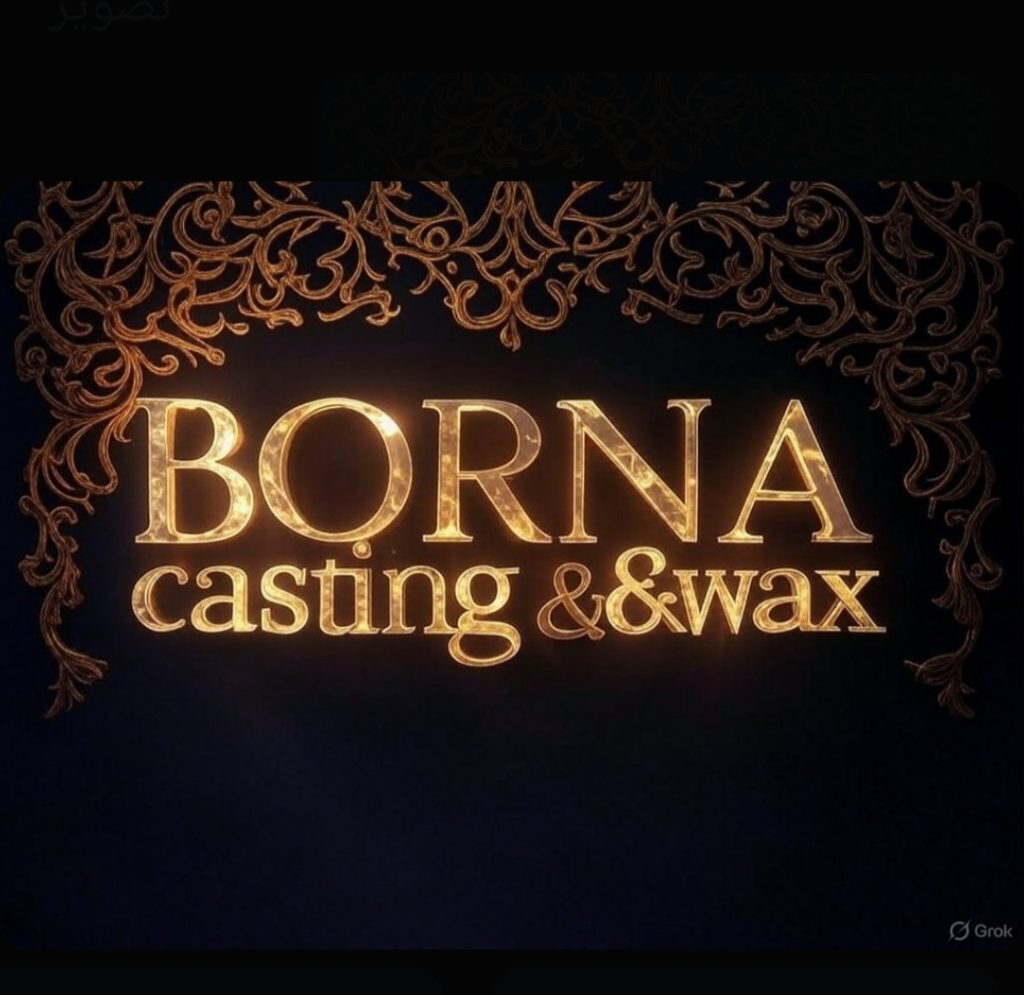
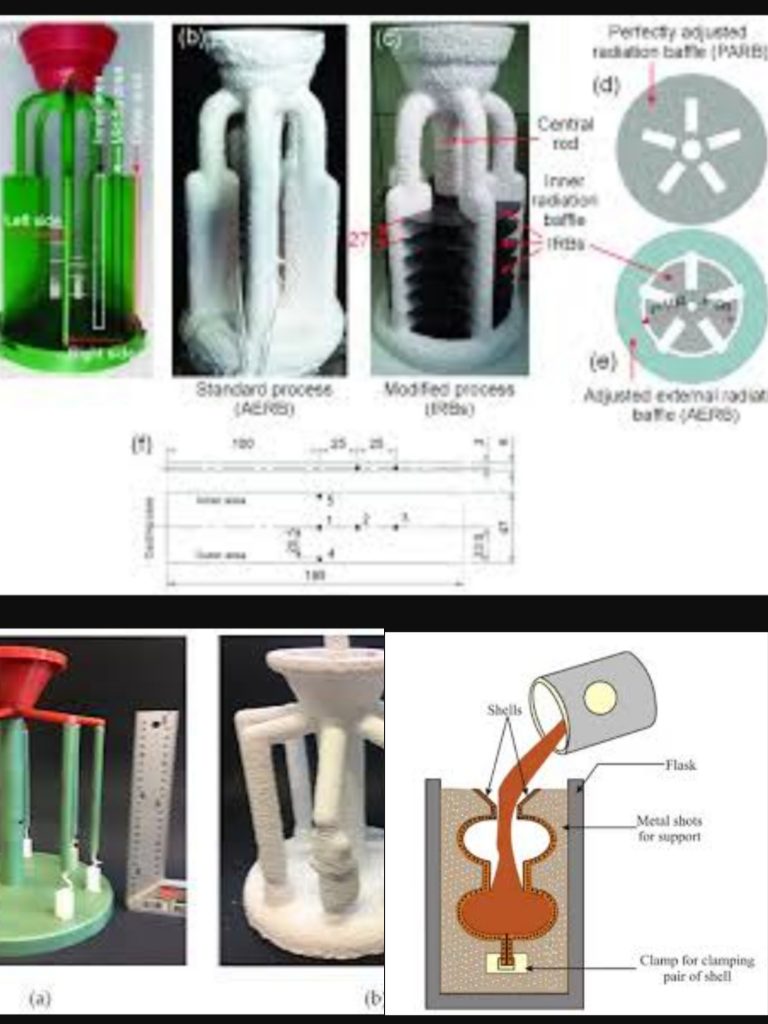